Industry 4.0: When a factory turns from a building into a data source
Every company and organisation operating today will face a common challenge at some point in their life cycle: the need to make their processes more efficient and thus achieve cost savings, thereby improving competitiveness.
The answer to this challenge is – not very surprisingly – digitalisation.
The digitalisation of companies’ operations has continued in industry and other sectors for years. It has been seen as a viable and sustainable solution to making processes more efficient and reducing their costs.
However, digitalisation is advancing at different paces in different sectors. Various service industries have been leading the way, while the manufacturing industry has been following suit at a more sluggish pace.
However, it is now the turn of a new era: a period of the rebirth, or renaissance, of the manufacturing industry is under way.
So what does the future of industry look like during and after the renaissance? What will a factory be like in 2030?
Industry 4.0 is the fourth revolution in places formerly called factories
The year 2030 may seem a long way off, yet it is only a little over seven years away from the present. We must therefore have a reasonably well-founded view of what lies ahead in 2030.
What we already know for sure is that industrial manufacturing is in the grips of the biggest change in decades. A factory is no longer just a building in the traditional sense, but factories and their processes are, at their core, turning into data sources generating huge masses of data, and gradually into entire ecosystems connecting raw material, production and distribution flows.
The concept of “Industry 4.0”, or the fourth industrial revolution, appears repeatedly in the visions of the manufacturing industry. It refers to a new phase of the industrial revolution with a strong focus on connectivity (hence the term IIoT, or industrial IoT), automation, machine learning, and real-time data. Industry 4.0 allows company management to better manage and understand each of their operations and make use of the immediate data accumulated from them to boost productivity, improve processes, and drive growth.
Industry 4.0 takes the focus of the digital development in recent decades to a whole new level by leveraging the connectivity offered by industrial IoT, access to real-time data, and the introduction of cyber-physical systems (combining physical and virtual operating environments). Industry 4.0 offers a much more comprehensive, interlinked and holistic approach to manufacturing than before. A holistic approach to manufacturing connects physical operations with digital ones and allows better collaboration and access between different departments, partners, vendors, products and people.
Technology is still our servant – People must evolve as the master
The driving force behind the creation of a new era of industrial manufacturing has been tremendous technological development. Behind Industry 4.0 are numerous technologies that bring increased productivity, such as:
- 5G;
- artificial intelligence;
- machine learning;
- super high resolution videography;
- increased big data structuring capability in the cloud; and
- augmented and assisted reality solutions.
Henri Viljasjärvi, Director, Business Development at Digita, helps us understand the new uses of technologies in the manufacturing industry through practical examples:
“One very concrete example is building a factory’s assembly lines on wireless communications, making them easily adaptable as the production process changes. Another example that I could mention is the transportation of material with an AGV trolley, an automatic forklift in the vernacular, from storage to the line. This can be used to increase the degree of automation and optimise the share of manual work.”
But – and this is a major but.
Industry 4.0 is not just about investing in new technologies and tools to increase the efficiency of manufacturing. It is a revolution of the company’s entire operations and growth.
Therefore, it is worth pointing out that in the future, too, technology will be our servant and people will still be in charge. But being in charge requires many new skills from people.
New requirements for knowledge work, data flows and information security
The transformation of factory work to become highly knowledge-intensive requires an unprecedented ability from a new generation of experts to reform manufacturing methods and operating models. In the future, a factory worker perceived through the traditional role will become more and more of a knowledge work professional.
As factory manufacturing becomes part of the data economy, the ability to think in new ways is needed. But simply thinking in a new way is not enough. A critical condition for the practical implementation of new methods is sufficient transmission and processing capacity for all the data flows that industry is able to collect with the help of sensors and other new aids. This allows data to be generated and transferred to the applications that will control production and material flows in the future, and connecting them to global logistics solutions and marketplaces.
Going forward, products and services will generate information and data throughout their life cycle, including after manufacturing – for example, on usage and wear. The challenge of the future is to keep security risks and infrastructure constantly protected and under control, fault-tolerant and, in some industries, up to a standard that ensures security of supply.
In addition to ever more skilled people, managing the big picture requires a secure solution that can be used to operate and control the factory, or rather a data unit focused on manufacturing in the future, in all conditions. There needs to be assurance that manufacturing will continue to operate amid energy crises, inflation and other threats of today.
One key solution to this is fast, wireless communication networks under the company’s own control, meaning private networks.
Private networks provide a versatile and safe platform for change in industry
A wireless private network serves as a versatile and safe guarantee of reliability as companies takes steps towards a production environment in accordance with Industry 4.0.
The increased automation and the utilisation of data enabled by wireless private networks increases the productivity of factories. In addition, the maintenance and upkeep of devices and machines can be speeded up and made more efficient, significantly reducing production interruptions in critical operations.
A fast, comprehensive and reliable network also increases safety, as it enables correct and extremely urgent measures to be taken in case of danger. It also makes reaching users and access control in danger areas more efficient than before.
Henri Viljasjärvi sums up the role of private networks in advancing the fourth industrial revolution as follows:
“With the help of a wireless private network built for internal use, companies can contribute to all the challenges posed by Industry 4.0. Private networks provide a versatile platform for digitalisation, and along with it, companies can effectively manage the security risks related to data transmission while improving operational cost-effectiveness. They are also suitable for many industrial uses: practically all spaces where the coverage, security and performance of a public mobile network or Wi-Fi network are not fully guaranteed are favourable targets for the introduction of a private network.”
Got any questions? Contact us and we’ll discuss what possibilities Private Network could offer for your company’s needs!
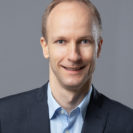